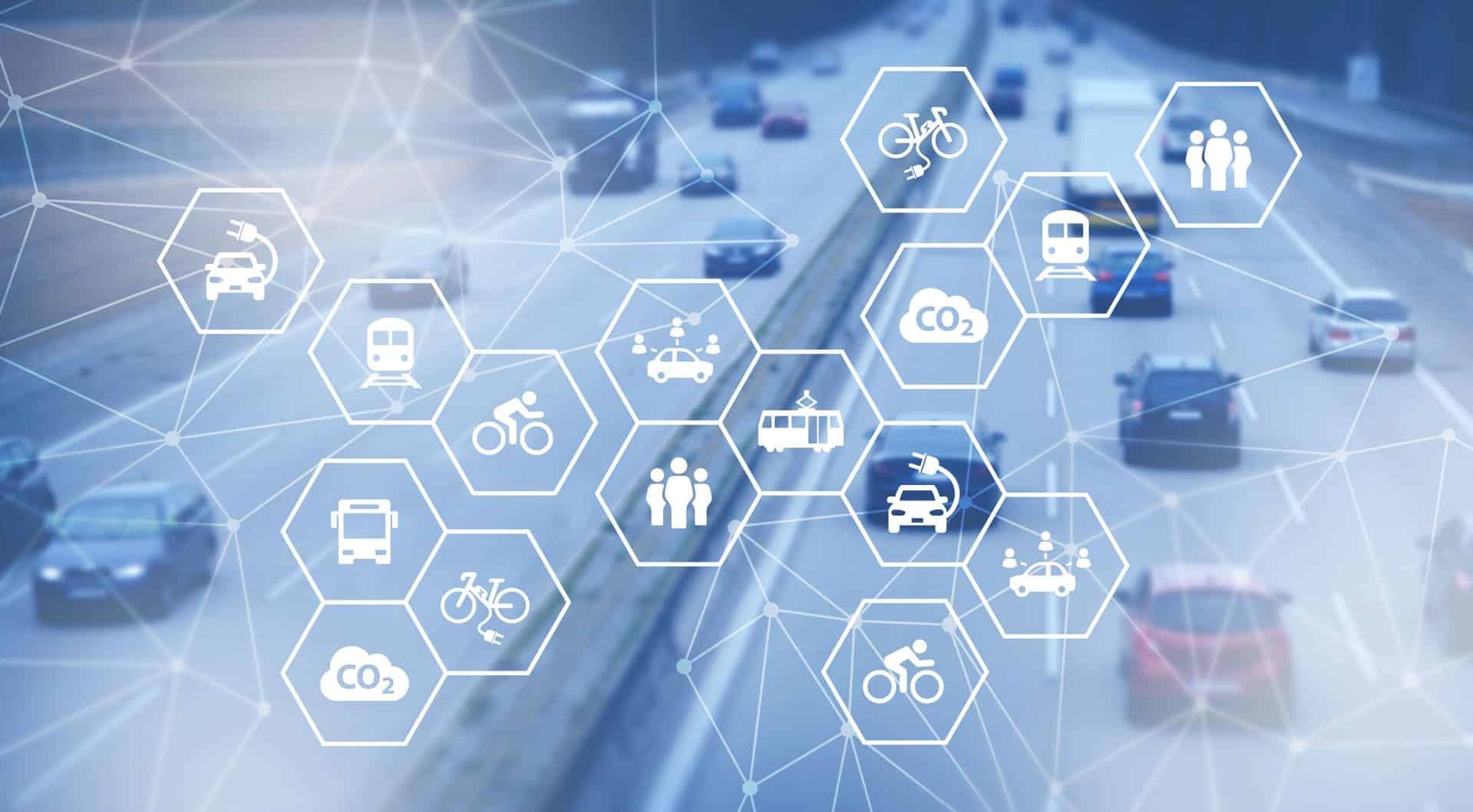
Applications
MatCHMaker’s ambition is to increase the industrial impact of materials bridging the gap between characterisation, modelling methods and rapid evaluation of materials. Within the project, requirements from industrial sectors will be translated into specific innovation challenges. The project results will be validated on three Use Cases.
Use Case I – Low-carbon Cement
To decrease the CO2 emission of cement production, substituting clinker with supplementary cementitious materials (SCM) is essential. Today, by-products of the steel and coal industries are heavily incorporated in the current European cements to that aim.
Tomorrow, because of the transition of the European Union out of the fossil fuel industry and the decarbonation of its steel industry, these SCMs will not be available anymore. Limestone and calcined clays are alternative SCMs that are abundant in the Earth crust and therefore available not just in Europe but across the globe.
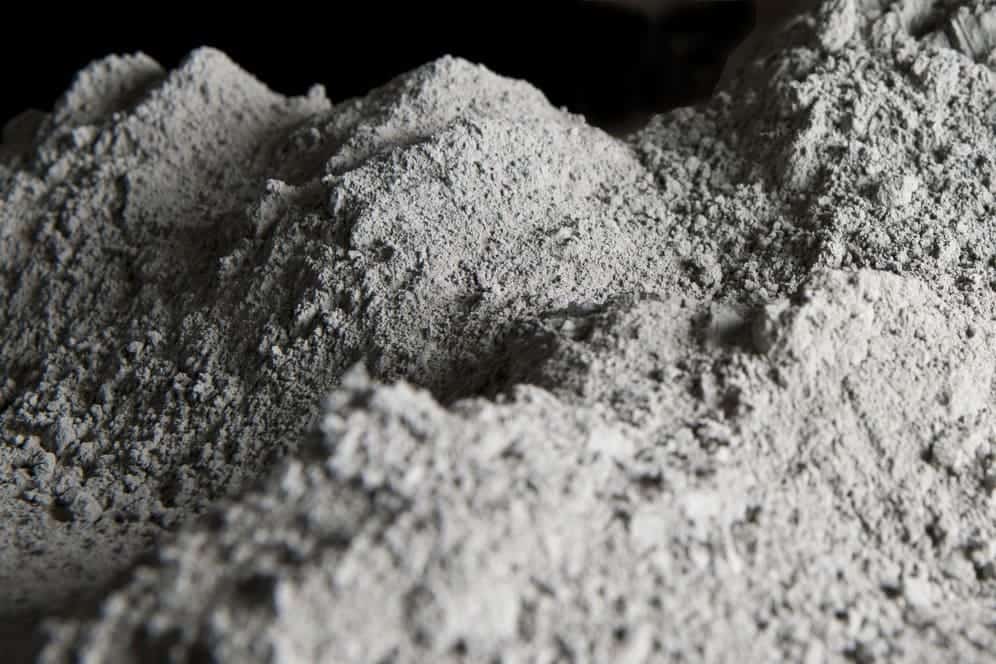
The challenge is therefore to find the maximum substitution level of clinker while maintaining equal or superior performance to the current product. The MatCHMaker project helps to build a predictive model for the strength of limestone calcined clay cements as a function of the replacement level, clinker mineralogy and fineness.
Through the collaboration with the CEA, MatCHMaker will enable the incorporation of the latest prediction and design of experiments machine learning (ML) methods in HeidelbergMaterials workflow, thus accelerating the development of new cements. The collaboration with TU WIEN IMWS will allow the benchmarking of novel methods with well-established physics-based methods.
The collaboration with AIMEN and SINTEF will provide the basis for generic image analysis ML methods for the class of cementitious materials. This basis will benefit the entire cement research community.
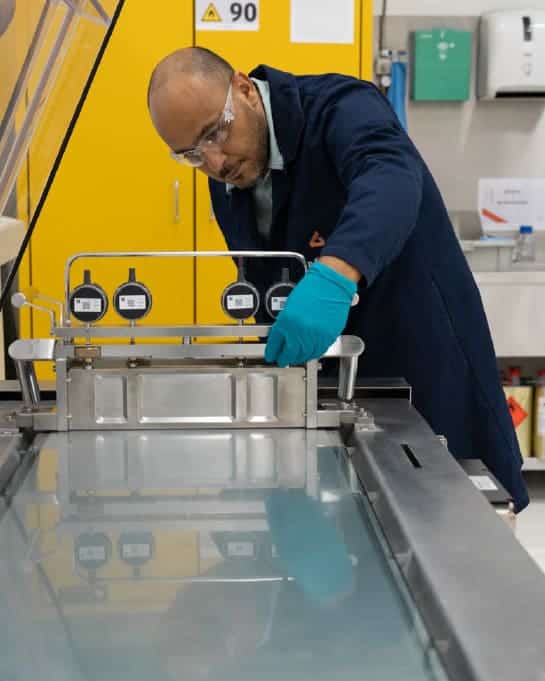
Use Case II - Solid Oxide Fuel Cells/Solid Oxide Electrolysis Cells (SOFC/SOEC)
To advance hydrogen production without CO2 emissions, electrolyser technologies producing hydrogen could meet the demands in various capacities. Our industrial partner Genvia is developing a high-efficiency solid oxide electrolyser technology allowing the production of decarbonised hydrogen for the industry.
Genvia is a clean hydrogen technology venture created to enable individual organisations, industries and nations to meet their goals for decarbonization by accelerating affordable clean hydrogen production, energy storage and fuel applications at scale. The company represents a unique combination of French science and global engineering, and benefits from the strength of a group of partner companies that include the French Alternative Energies and Atomic Energy Commission (CEA), SLB New Energy, VINCI Construction, Vicat Group and the Occitanie Region.
Genvia develops the next generation of electrolyser technology to produce hydrogen without CO2 emissions. The technology aims to achieve the highest system efficiency, resulting in significantly less electricity use per kg of hydrogen produced. The technology is the first of its kind that is fully reversible, giving it the flexibility to switch between electrolysis and fuel cell functions.
The technology is based on multi-scale components.
Within the MatCHMaker project, focusing on cell technology, the aim is to improve the performance and mechanical robustness of electrochemical cells implemented in SOEC/SOFC via advanced modelling and characterisation.
Use Case III – Proton-Exchange Membrane Fuel Cells (PEMFC)
Analytical and computational tools enable a better understanding of degradation in fuel cells. The MatCHMaker project aims to develop new future high-performance material by enhancing computational analysis in this use case. Together with Toyota Motor Europe, the project focuses on improving the durability and performance of proton-exchange membrane fuel cells (PEMFC) for mobility applications (heavy-duty, lightweight vehicles etc.).
Toyota is at the forefront of hydrogen technology innovation, having introduced the Mirai, the world’s first commercialised hydrogen fuel cell electric sedan, in 2014. Since then, the development of the Toyota fuel cell system has continued, making it more compact, lighter, and yet also more energy dense. In 2021, the comprehensively improved system will debut in the next generation of Mirai.
Toyota’s technology is flexible to be used in cars and to produce zero-emission power in multiple applications. It is already powering trucks, urban bus fleets, forklifts and generators. Tests are also underway for applications in boats and trains.
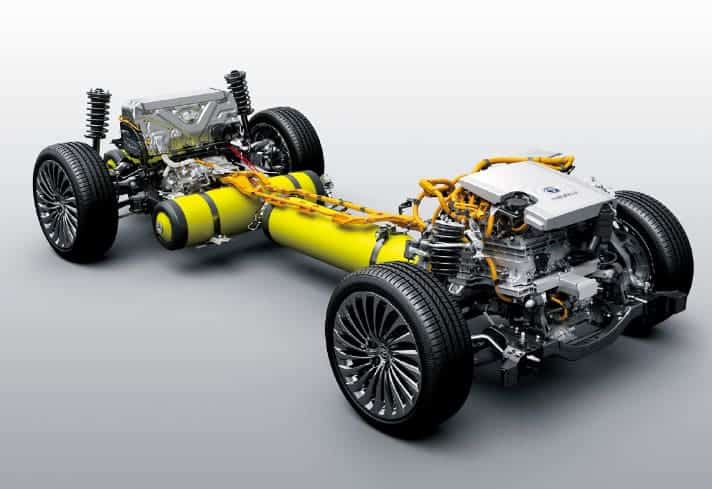